Destylator przemysłowy to urządzenie, które odgrywa kluczową rolę w wielu procesach produkcyjnych, szczególnie w przemyśle chemicznym i petrochemicznym. Jego głównym zadaniem jest oddzielanie składników mieszanin cieczy na podstawie różnicy w ich temperaturach wrzenia. Proces destylacji polega na podgrzewaniu cieczy do momentu, gdy jeden z jej składników zaczyna parować, a następnie schładzaniu pary, aby skondensować ją z powrotem do stanu ciekłego. W przemyśle często stosuje się różne typy destylatorów, w tym destylatory prostokątne oraz kolumnowe, które różnią się konstrukcją i zastosowaniem. W przypadku destylacji kolumnowej, proces ten jest bardziej efektywny, ponieważ pozwala na wielokrotne skraplanie i parowanie, co zwiększa czystość uzyskiwanych produktów.
Jakie są rodzaje destylatorów przemysłowych dostępnych na rynku
Na rynku dostępnych jest wiele rodzajów destylatorów przemysłowych, które różnią się zarówno konstrukcją, jak i przeznaczeniem. Wśród najpopularniejszych typów można wymienić destylatory prostokątne, kolumnowe oraz wirówkowe. Destylatory prostokątne są najczęściej stosowane w małych zakładach produkcyjnych i laboratoriach, gdzie wymagane są niewielkie ilości destylatu. Z kolei destylatory kolumnowe charakteryzują się większą wydajnością i są wykorzystywane w dużych zakładach przemysłowych do produkcji substancji chemicznych oraz paliw. Destylatory wirówkowe natomiast znajdują zastosowanie w przemyśle spożywczym, gdzie służą do oddzielania składników w produktach takich jak oleje czy soki. Każdy z tych typów ma swoje unikalne cechy i zalety, które sprawiają, że są one odpowiednie do różnych zastosowań.
Jakie zastosowania mają destylatory przemysłowe w różnych branżach
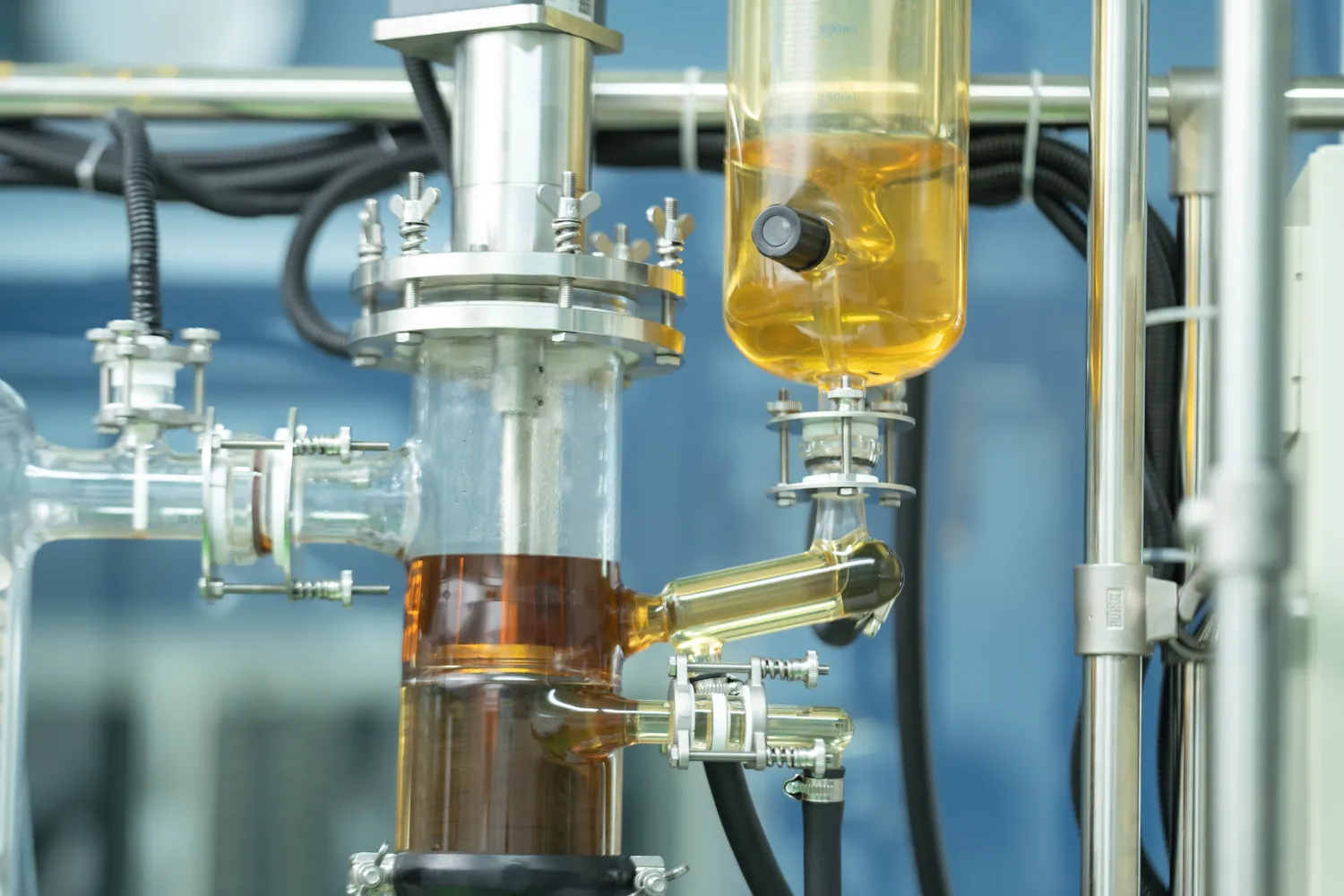
Destylatory przemysłowe znajdują szerokie zastosowanie w różnych branżach gospodarki, od przemysłu chemicznego po spożywczy. W przemyśle chemicznym destylacja jest kluczowym procesem przy produkcji wielu substancji chemicznych, takich jak rozpuszczalniki, kwasy czy alkohole. W branży petrochemicznej destylatory są wykorzystywane do rafinacji ropy naftowej, co pozwala na uzyskanie różnych frakcji paliwowych oraz innych produktów naftowych. W przemyśle spożywczym destylacja jest niezbędna do produkcji napojów alkoholowych oraz aromatów. Na przykład w produkcji whisky czy wina proces ten pozwala na uzyskanie pożądanej mocy trunku oraz jego charakterystycznego smaku. Ponadto destylatory znajdują również zastosowanie w farmaceutyce, gdzie służą do oczyszczania substancji czynnych oraz ich ekstrakcji z surowców roślinnych.
Jakie są kluczowe elementy konstrukcyjne destylatora przemysłowego
Konstrukcja destylatora przemysłowego opiera się na kilku kluczowych elementach, które zapewniają jego prawidłowe funkcjonowanie. Podstawowym elementem jest zbiornik do podgrzewania cieczy, który umożliwia osiągnięcie odpowiedniej temperatury wrzenia dla poszczególnych składników mieszaniny. Kolejnym istotnym elementem jest kolumna destylacyjna, która pełni funkcję separacyjną i umożliwia wielokrotne skraplanie oraz parowanie substancji. W górnej części kolumny znajduje się skraplacz, który schładza parę i przekształca ją z powrotem w ciecz. Dodatkowo wiele nowoczesnych destylatorów wyposażonych jest w systemy automatyzacji i monitoringu, które pozwalają na precyzyjne kontrolowanie parametrów procesu oraz optymalizację wydajności urządzenia. Ważnym aspektem konstrukcyjnym jest również materiał wykonania poszczególnych elementów, który powinien być odporny na działanie wysokich temperatur oraz korozję chemiczną.
Jakie są wyzwania związane z eksploatacją destylatorów przemysłowych
Eksploatacja destylatorów przemysłowych wiąże się z szeregiem wyzwań technicznych oraz operacyjnych, które mogą wpływać na efektywność procesu produkcyjnego. Jednym z głównych problemów jest konieczność utrzymania odpowiednich warunków pracy urządzenia, takich jak temperatura czy ciśnienie wewnętrzne. Niewłaściwe parametry mogą prowadzić do obniżenia wydajności lub nawet uszkodzenia sprzętu. Kolejnym wyzwaniem jest konieczność regularnego czyszczenia i konserwacji destylatorów, aby zapobiec osadzaniu się zanieczyszczeń oraz poprawić jakość uzyskiwanego produktu. Dodatkowo operatorzy muszą być dobrze przeszkoleni w zakresie obsługi urządzeń oraz reagowania na ewentualne awarie czy nieprawidłowości w pracy systemu. Warto również zwrócić uwagę na aspekty ekologiczne związane z eksploatacją destylatorów, takie jak emisja gazów czy zużycie energii.
Jakie są koszty związane z zakupem destylatora przemysłowego
Koszty zakupu destylatora przemysłowego mogą się znacznie różnić w zależności od wielu czynników, takich jak typ urządzenia, jego wydajność oraz zastosowane technologie. W przypadku prostych destylatorów laboratoryjnych ceny mogą zaczynać się od kilku tysięcy złotych, podczas gdy bardziej zaawansowane systemy kolumnowe przeznaczone do dużych zakładów przemysłowych mogą kosztować setki tysięcy, a nawet miliony złotych. Dodatkowo, przy ocenie całkowitych kosztów zakupu należy uwzględnić także wydatki związane z instalacją, uruchomieniem oraz szkoleniem personelu. Koszty eksploatacji destylatora również powinny być brane pod uwagę, ponieważ obejmują one zużycie energii, konserwację oraz ewentualne naprawy. Warto także rozważyć długoterminowe oszczędności wynikające z efektywności energetycznej nowoczesnych urządzeń, które mogą zredukować koszty operacyjne w perspektywie kilku lat.
Jakie są najnowsze technologie w dziedzinie destylacji przemysłowej
W ostatnich latach w dziedzinie destylacji przemysłowej pojawiło się wiele innowacyjnych technologii, które mają na celu poprawę efektywności procesów oraz redukcję kosztów produkcji. Jednym z najważniejszych trendów jest automatyzacja procesów destylacyjnych, która pozwala na precyzyjne monitorowanie i kontrolowanie parametrów pracy urządzenia. Dzięki zastosowaniu zaawansowanych systemów sterowania możliwe jest dostosowywanie warunków pracy do zmieniających się właściwości surowców oraz uzyskiwanie lepszej jakości produktów końcowych. Kolejnym istotnym osiągnięciem jest rozwój technologii membranowych, które umożliwiają separację składników mieszanin bez konieczności ich podgrzewania, co prowadzi do znacznego zmniejszenia zużycia energii. Innowacyjne podejścia do projektowania kolumn destylacyjnych, takie jak wykorzystanie materiałów kompozytowych czy nanotechnologii, również przyczyniają się do zwiększenia efektywności procesów.
Jakie są kluczowe czynniki wpływające na wydajność destylatora przemysłowego
Wydajność destylatora przemysłowego jest determinowana przez szereg czynników, które mają wpływ na skuteczność procesu separacji składników. Jednym z najważniejszych elementów jest temperatura wrzenia poszczególnych składników mieszaniny, która wpływa na szybkość parowania i skraplania. Odpowiednie dobranie warunków pracy, takich jak ciśnienie czy temperatura w kolumnie destylacyjnej, ma kluczowe znaczenie dla uzyskania wysokiej czystości produktów. Kolejnym czynnikiem jest konstrukcja samego urządzenia – kolumny o większej liczbie teoretycznych półek pozwalają na lepszą separację składników i zwiększenie wydajności procesu. Również jakość surowców ma znaczenie; obecność zanieczyszczeń czy niejednorodność składu może negatywnie wpłynąć na efektywność destylacji. Ważne jest również odpowiednie utrzymanie sprzętu w dobrym stanie technicznym oraz regularne przeprowadzanie konserwacji, co pozwala na uniknięcie awarii i zapewnienie ciągłości produkcji.
Jakie są różnice między destylacją prostą a frakcyjną w przemyśle
Destylacja prosta i frakcyjna to dwa podstawowe rodzaje procesów stosowanych w przemyśle chemicznym do separacji składników cieczy. Destylacja prosta polega na jednorazowym podgrzewaniu mieszaniny i skraplaniu pary bez dodatkowych etapów separacji. Jest to metoda stosunkowo prosta i tania, jednak jej zastosowanie ogranicza się głównie do sytuacji, gdy różnica temperatur wrzenia składników jest znaczna. Z kolei destylacja frakcyjna to bardziej zaawansowany proces, który wykorzystuje kolumny destylacyjne do wielokrotnego skraplania i parowania substancji. Dzięki temu możliwe jest uzyskanie wyższej czystości produktów oraz lepsza separacja składników o zbliżonych temperaturach wrzenia. Destylacja frakcyjna jest powszechnie stosowana w przemyśle petrochemicznym do rafinacji ropy naftowej oraz w produkcji alkoholu wysokoprocentowego.
Jakie są korzyści z inwestycji w nowoczesne destylatory przemysłowe
Inwestycja w nowoczesne destylatory przemysłowe przynosi wiele korzyści zarówno dla producentów, jak i dla środowiska naturalnego. Przede wszystkim nowoczesne urządzenia charakteryzują się wyższą efektywnością energetyczną, co przekłada się na niższe koszty eksploatacji oraz mniejsze zużycie surowców. Dzięki zastosowaniu innowacyjnych technologii możliwe jest osiągnięcie lepszej jakości produktów końcowych oraz zwiększenie wydajności procesów produkcyjnych. Nowoczesne destylatory często wyposażone są w systemy automatyzacji i monitoringu, co pozwala na precyzyjne kontrolowanie parametrów pracy oraz szybsze reagowanie na ewentualne problemy. Dodatkowo inwestycje te mogą przyczynić się do poprawy bezpieczeństwa pracy w zakładzie poprzez zastosowanie nowoczesnych rozwiązań inżynieryjnych oraz technologicznych.
Jakie są przyszłe trendy w rozwoju technologii destylacyjnej
Przyszłość technologii destylacyjnej zapowiada się obiecująco dzięki ciągłemu rozwojowi innowacyjnych rozwiązań oraz rosnącemu zainteresowaniu ekologicznymi metodami produkcji. Jednym z kluczowych trendów jest dalsza automatyzacja procesów produkcyjnych, co pozwoli na jeszcze większą precyzję i efektywność operacyjną. Zastosowanie sztucznej inteligencji i uczenia maszynowego może przyczynić się do optymalizacji parametrów pracy urządzeń oraz przewidywania awarii zanim one wystąpią. Również rozwój technologii membranowych i innych alternatywnych metod separacji może wpłynąć na zmniejszenie zapotrzebowania na tradycyjne metody destylacji, co przyczyni się do oszczędności energetycznych i redukcji emisji gazów cieplarnianych. W kontekście rosnącej konkurencji rynkowej firmy będą musiały inwestować w innowacje technologiczne, aby utrzymać swoją pozycję na rynku oraz sprostać wymaganiom klientów dotyczących jakości produktów i ochrony środowiska.