Falowniki to urządzenia, które odgrywają kluczową rolę w przekształcaniu energii elektrycznej. Ich głównym zadaniem jest konwersja prądu stałego na prąd zmienny, co jest niezbędne w wielu zastosowaniach przemysłowych oraz w systemach odnawialnych źródeł energii. W praktyce falowniki znajdują zastosowanie w napędach silników elektrycznych, systemach fotowoltaicznych oraz w różnych aplikacjach automatyki. Działanie falownika opiera się na modulacji szerokości impulsów, co pozwala na regulację częstotliwości i napięcia wyjściowego. Dzięki temu możliwe jest precyzyjne sterowanie prędkością obrotową silników oraz dostosowywanie parametrów pracy do wymagań konkretnego procesu technologicznego. Warto zaznaczyć, że nowoczesne falowniki są wyposażone w zaawansowane funkcje diagnostyczne oraz komunikacyjne, co umożliwia ich integrację z systemami zarządzania energią i automatyki przemysłowej.
Jakie są rodzaje falowników i ich zastosowania
Falowniki można podzielić na kilka kategorii w zależności od ich zastosowania oraz konstrukcji. Najpopularniejsze typy to falowniki jednofazowe oraz trójfazowe, które różnią się liczbą faz wyjściowych. Falowniki jednofazowe są często stosowane w małych aplikacjach domowych, takich jak systemy fotowoltaiczne czy napędy małych silników. Z kolei falowniki trójfazowe znajdują zastosowanie w większych instalacjach przemysłowych, gdzie wymagane są wyższe moce i lepsza stabilność pracy. Innym ważnym podziałem jest klasyfikacja według sposobu modulacji sygnału, wyróżniamy falowniki PWM (modulacja szerokości impulsów) oraz falowniki z modulacją wektora. Falowniki PWM są najczęściej stosowane ze względu na swoją prostotę i efektywność, natomiast falowniki z modulacją wektora oferują lepszą kontrolę nad momentem obrotowym silnika.
Jakie korzyści przynoszą falowniki w codziennym użytkowaniu
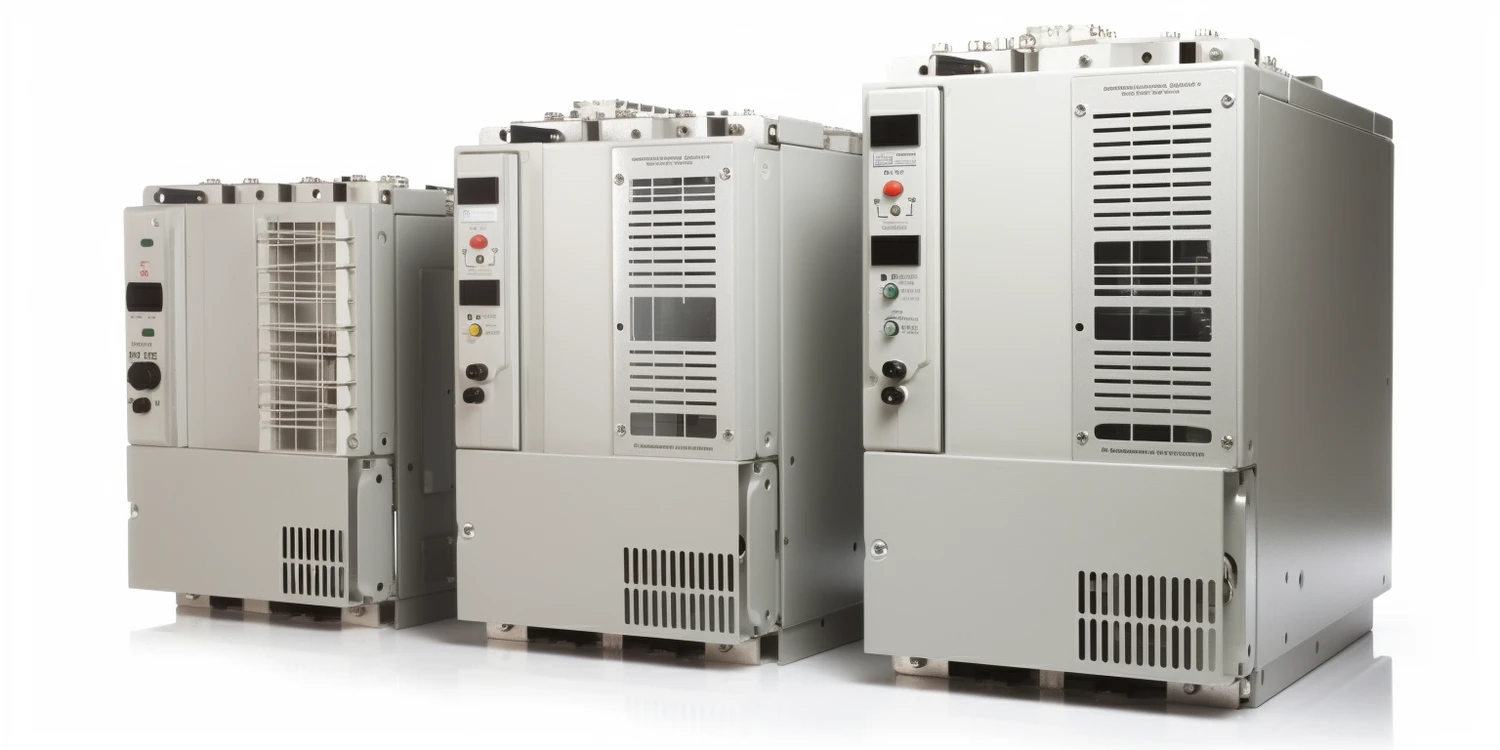
Wykorzystanie falowników w codziennym użytkowaniu przynosi szereg korzyści zarówno dla użytkowników indywidualnych, jak i dla przedsiębiorstw. Przede wszystkim pozwalają one na oszczędność energii poprzez optymalizację pracy urządzeń elektrycznych. Dzięki możliwości regulacji prędkości obrotowej silników, falowniki przyczyniają się do zmniejszenia zużycia energii, co jest szczególnie istotne w przypadku długotrwałego użytkowania maszyn przemysłowych. Dodatkowo falowniki mogą wydłużać żywotność urządzeń elektrycznych poprzez eliminację niekorzystnych skoków napięcia oraz zmniejszenie obciążeń mechanicznych. W kontekście odnawialnych źródeł energii, takich jak panele słoneczne czy turbiny wiatrowe, falowniki umożliwiają efektywne wykorzystanie wyprodukowanej energii poprzez jej konwersję do formatu zgodnego z siecią energetyczną.
Jakie są najnowsze trendy w technologii falowników
Technologia falowników rozwija się dynamicznie, a najnowsze trendy koncentrują się na zwiększeniu efektywności energetycznej oraz integracji z inteligentnymi systemami zarządzania energią. W ostatnich latach zauważalny jest wzrost zainteresowania falownikami o wysokiej wydajności, które charakteryzują się mniejszymi stratami energii oraz lepszymi parametrami pracy. W kontekście odnawialnych źródeł energii rośnie znaczenie falowników hybrydowych, które łączą funkcje konwersji energii z możliwością magazynowania jej w akumulatorach. Ponadto coraz większą rolę odgrywają technologie komunikacyjne, takie jak IoT (Internet of Things), które pozwalają na zdalne monitorowanie i zarządzanie pracą falowników w czasie rzeczywistym. Dzięki temu możliwe jest optymalizowanie procesów produkcyjnych oraz minimalizacja kosztów eksploatacyjnych.
Jakie są kluczowe elementy falowników i ich funkcje
Falowniki składają się z kilku kluczowych elementów, które współpracują ze sobą, aby zapewnić prawidłowe działanie urządzenia. Jednym z najważniejszych komponentów jest prostownik, który przekształca prąd zmienny na prąd stały. Prostownik może być realizowany w różnych konfiguracjach, w tym w układzie jednofazowym lub trójfazowym, co wpływa na efektywność konwersji energii. Kolejnym istotnym elementem jest układ filtrów, który ma na celu eliminację zakłóceń elektromagnetycznych oraz wygładzanie napięcia wyjściowego. Filtry te są niezbędne do zapewnienia stabilnej pracy falownika oraz ochrony podłączonych urządzeń przed szkodliwymi skutkami impulsów napięcia. Następnie mamy do czynienia z modułem sterującym, który odpowiada za kontrolę pracy falownika oraz jego interakcję z innymi systemami. Moduł ten często zawiera algorytmy regulacji, które pozwalają na optymalizację parametrów pracy w czasie rzeczywistym. Ostatnim istotnym elementem jest interfejs komunikacyjny, który umożliwia integrację falownika z systemami zarządzania energią oraz automatyki przemysłowej.
Jakie są wyzwania związane z użytkowaniem falowników
Pomimo licznych korzyści płynących z zastosowania falowników, istnieją również pewne wyzwania związane z ich użytkowaniem. Jednym z głównych problemów jest kwestia kompatybilności z różnymi typami urządzeń elektrycznych. Nie wszystkie silniki czy systemy są przystosowane do pracy z falownikami, co może prowadzić do problemów z wydajnością lub nawet uszkodzeniem sprzętu. Dodatkowo, falowniki mogą generować zakłócenia elektromagnetyczne, które mogą wpływać na działanie innych urządzeń w pobliżu. W związku z tym konieczne jest stosowanie odpowiednich filtrów oraz zabezpieczeń, aby minimalizować te negatywne skutki. Innym wyzwaniem jest potrzeba regularnej konserwacji i monitorowania stanu technicznego falowników, co wiąże się z dodatkowymi kosztami operacyjnymi dla przedsiębiorstw. Warto również zwrócić uwagę na kwestie związane z instalacją i uruchomieniem falowników, które wymagają specjalistycznej wiedzy oraz doświadczenia.
Jakie są przyszłościowe kierunki rozwoju technologii falowników
Przyszłość technologii falowników rysuje się w jasnych barwach dzięki dynamicznemu rozwojowi branży energetycznej oraz rosnącemu zapotrzebowaniu na efektywność energetyczną. Jednym z kluczowych kierunków rozwoju jest integracja falowników z systemami odnawialnych źródeł energii, co pozwoli na jeszcze lepsze wykorzystanie energii słonecznej i wiatrowej. W miarę jak technologia baterii staje się coraz bardziej zaawansowana i dostępna, falowniki hybrydowe będą odgrywać coraz większą rolę w magazynowaniu energii oraz jej późniejszym wykorzystaniu w gospodarstwach domowych i przemyśle. Kolejnym ważnym trendem jest rozwój inteligentnych systemów zarządzania energią, które pozwolą na optymalizację zużycia energii w czasie rzeczywistym oraz integrację różnych źródeł energii w jedną spójną sieć. W kontekście przemysłu 4.0 rośnie znaczenie komunikacji międzyfalownikowej oraz integracji z systemami IoT, co umożliwi jeszcze lepsze monitorowanie i zarządzanie pracą urządzeń elektrycznych.
Jakie są zastosowania falowników w różnych branżach przemysłowych
Falowniki znajdują szerokie zastosowanie w różnych branżach przemysłowych, od produkcji po transport i energetykę. W sektorze produkcyjnym falowniki są wykorzystywane do napędzania silników elektrycznych w maszynach takich jak pompy, wentylatory czy kompresory. Dzięki możliwości regulacji prędkości obrotowej silników można dostosować wydajność maszyn do aktualnych potrzeb produkcyjnych, co przekłada się na oszczędność energii i zwiększenie efektywności procesów technologicznych. W branży transportowej falowniki odgrywają kluczową rolę w napędach elektrycznych pojazdów szynowych oraz tramwajów, gdzie precyzyjna kontrola prędkości jest niezbędna dla bezpieczeństwa i komfortu pasażerów. W sektorze energetycznym falowniki są niezbędne do integracji odnawialnych źródeł energii z siecią elektroenergetyczną, umożliwiając konwersję energii słonecznej czy wiatrowej na formę użyteczną dla odbiorców końcowych.
Jakie są koszty związane z zakupem i eksploatacją falowników
Koszty związane z zakupem i eksploatacją falowników mogą się znacznie różnić w zależności od ich typu, mocy oraz zastosowania. Na etapie zakupu warto zwrócić uwagę nie tylko na cenę samego urządzenia, ale także na dodatkowe koszty związane z instalacją oraz konfiguracją systemu. W przypadku bardziej zaawansowanych modeli może być konieczne zatrudnienie specjalistów do przeprowadzenia instalacji oraz uruchomienia falownika, co generuje dodatkowe wydatki. Koszty eksploatacyjne obejmują zarówno zużycie energii przez sam falownik, jak i ewentualne koszty konserwacji oraz naprawy urządzenia w przypadku awarii. Regularna konserwacja jest kluczowa dla zapewnienia długotrwałej pracy falownika oraz minimalizacji ryzyka wystąpienia problemów technicznych. Warto również uwzględnić potencjalne oszczędności wynikające z zastosowania falowników w procesach produkcyjnych czy systemach energetycznych, które mogą znacznie przewyższyć początkowe inwestycje.
Jakie są opinie użytkowników dotyczące falowników
Opinie użytkowników dotyczące falowników są zazwyczaj pozytywne, zwłaszcza jeśli chodzi o ich wpływ na efektywność energetyczną oraz oszczędności kosztów operacyjnych. Użytkownicy często podkreślają korzyści płynące z możliwości precyzyjnego sterowania prędkością obrotową silników oraz dostosowywania parametrów pracy do aktualnych potrzeb produkcyjnych czy energetycznych. Wiele osób zauważa również poprawę jakości pracy urządzeń elektrycznych dzięki eliminacji skoków napięcia oraz zmniejszeniu obciążeń mechanicznych. Jednak niektórzy użytkownicy wskazują również na pewne trudności związane z instalacją i konfiguracją falowników, które mogą wymagać specjalistycznej wiedzy oraz doświadczenia. Problemy te mogą być szczególnie uciążliwe dla mniejszych przedsiębiorstw bez dostępu do odpowiednich zasobów technicznych.