Automatyzacja w przemyśle przynosi wiele korzyści, które mają znaczący wpływ na efektywność produkcji oraz jakość wytwarzanych produktów. Przede wszystkim, automatyzacja pozwala na zwiększenie wydajności procesów produkcyjnych, co przekłada się na szybsze tempo pracy i możliwość realizacji większej liczby zamówień. Dzięki zastosowaniu nowoczesnych technologii, takich jak roboty przemysłowe czy systemy zarządzania produkcją, przedsiębiorstwa mogą zredukować czas cyklu produkcyjnego oraz minimalizować przestoje. Kolejną istotną zaletą jest poprawa jakości produktów, ponieważ automatyzacja eliminuje błędy ludzkie, co prowadzi do bardziej jednolitych i precyzyjnych wyników. Dodatkowo, automatyzacja przyczynia się do obniżenia kosztów operacyjnych poprzez zmniejszenie zapotrzebowania na pracowników w niektórych obszarach, co z kolei pozwala na alokację zasobów w bardziej strategiczne miejsca.
Jakie technologie są wykorzystywane w automatyzacji przemysłowej
W automatyzacji przemysłowej wykorzystuje się szereg nowoczesnych technologii, które mają na celu usprawnienie procesów produkcyjnych oraz zwiększenie ich efektywności. Jednym z najważniejszych elementów są roboty przemysłowe, które wykonują powtarzalne zadania z dużą precyzją i szybkością. Roboty te mogą być programowane do różnych zadań, od montażu po pakowanie, co sprawia, że są niezwykle wszechstronne. Kolejną kluczową technologią są systemy sterowania procesami, które umożliwiają monitorowanie i zarządzanie różnymi etapami produkcji w czasie rzeczywistym. Dzięki tym systemom można szybko reagować na zmiany oraz optymalizować procesy. Warto również wspomnieć o sztucznej inteligencji i uczeniu maszynowym, które coraz częściej znajdują zastosowanie w analizie danych produkcyjnych oraz prognozowaniu awarii maszyn. Internet rzeczy (IoT) to kolejny trend, który umożliwia łączenie urządzeń i maszyn w sieci, co pozwala na zbieranie danych i ich analizę w celu dalszej optymalizacji procesów.
Jakie wyzwania wiążą się z automatyzacją w przemyśle
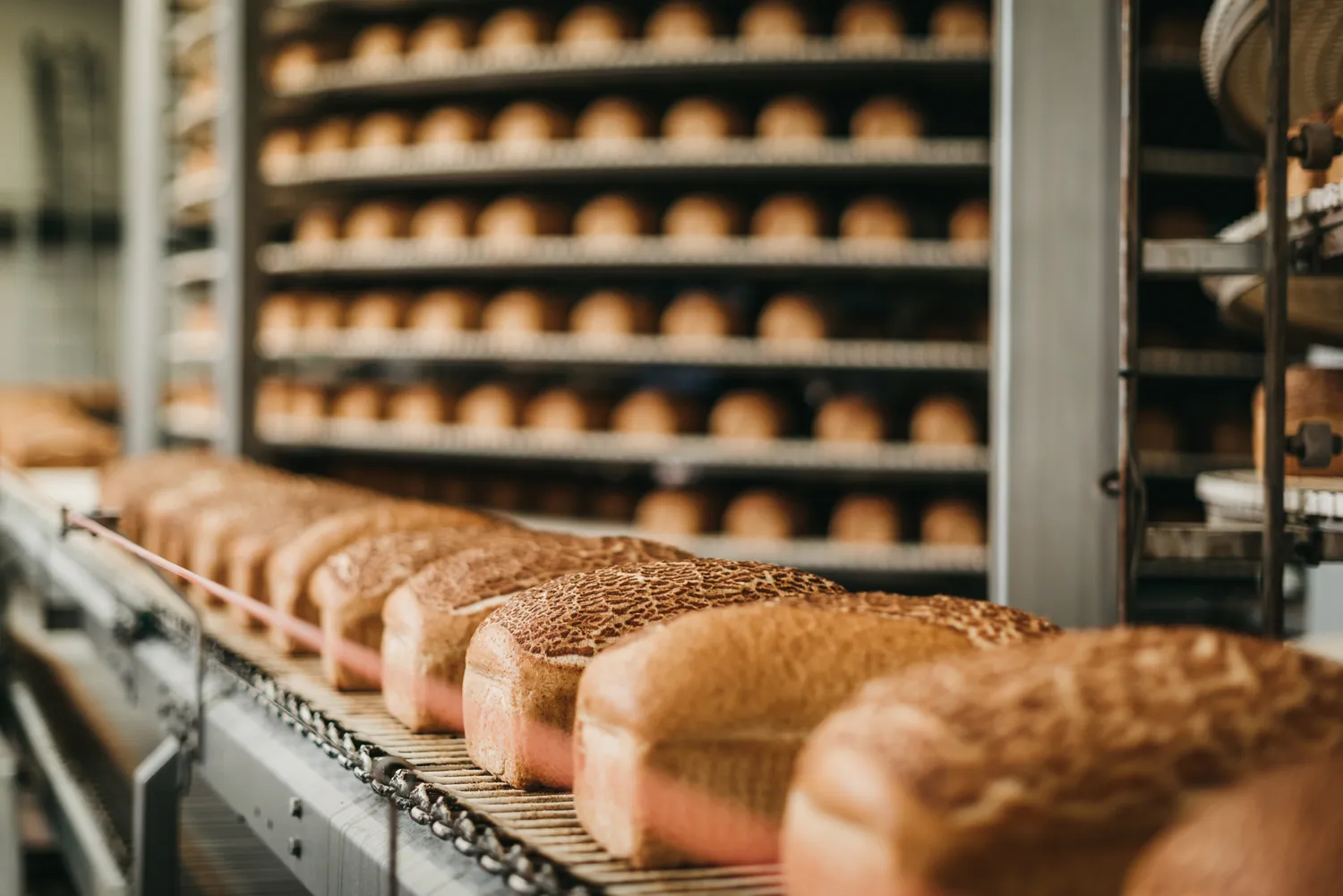
Pomimo licznych korzyści płynących z automatyzacji w przemyśle, istnieje także szereg wyzwań, które przedsiębiorstwa muszą stawić czoła podczas wdrażania nowych technologii. Jednym z głównych problemów jest wysoki koszt początkowy inwestycji w nowoczesne maszyny i systemy automatyzacji. Dla wielu firm może to stanowić barierę wejścia, zwłaszcza dla małych i średnich przedsiębiorstw. Kolejnym wyzwaniem jest konieczność przeszkolenia pracowników do obsługi nowych technologii oraz dostosowania ich umiejętności do zmieniającego się środowiska pracy. Wprowadzenie automatyzacji często wiąże się także z obawami o utratę miejsc pracy przez pracowników wykonujących rutynowe zadania. Firmy muszą więc znaleźć równowagę pomiędzy automatyzacją a zatrudnieniem ludzi, co może być trudne do osiągnięcia. Ponadto, wdrażanie nowych technologii wiąże się z ryzykiem awarii systemów oraz problemami związanymi z integracją różnych rozwiązań technologicznych.
Jakie są przyszłe trendy w automatyzacji przemysłu
Przemysłowy krajobraz automatyzacji stale ewoluuje i pojawiają się nowe trendy, które mają potencjał do dalszej transformacji tego sektora. Jednym z najważniejszych kierunków rozwoju jest integracja sztucznej inteligencji i uczenia maszynowego w procesach produkcyjnych. Dzięki tym technologiom możliwe będzie nie tylko lepsze prognozowanie potrzeb produkcyjnych, ale także samodzielne podejmowanie decyzji przez maszyny na podstawie analizy danych. Również rozwój robotyki współpracującej staje się coraz bardziej popularny; roboty te mogą pracować obok ludzi bez potrzeby oddzielania ich od siebie barierami ochronnymi, co zwiększa elastyczność linii produkcyjnej. Inwestycje w Internet rzeczy (IoT) będą również kluczowe dla przyszłości automatyzacji; dzięki połączeniu maszyn i urządzeń możliwe będzie zbieranie ogromnych ilości danych oraz ich analiza w czasie rzeczywistym. W kontekście zrównoważonego rozwoju rośnie także zainteresowanie technologiami energooszczędnymi oraz rozwiązaniami przyjaznymi dla środowiska. Automatyzacja może odegrać istotną rolę w redukcji odpadów oraz optymalizacji zużycia energii w procesach produkcyjnych.
Jak automatyzacja wpływa na jakość produktów w przemyśle
Automatyzacja w przemyśle ma kluczowy wpływ na jakość produktów, co jest jednym z głównych powodów, dla których przedsiębiorstwa decydują się na wdrożenie nowoczesnych technologii. Dzięki zastosowaniu robotów i systemów automatyzacji, procesy produkcyjne stają się bardziej precyzyjne i powtarzalne, co minimalizuje ryzyko wystąpienia błędów ludzkich. W przypadku ręcznej produkcji, nawet drobne pomyłki mogą prowadzić do wadliwych produktów, które generują dodatkowe koszty związane z reklamacjami i zwrotami. Automatyzacja eliminuje te problemy poprzez wprowadzenie standardowych procedur operacyjnych, które są niezmienne i dokładnie kontrolowane przez maszyny. Dodatkowo, nowoczesne technologie umożliwiają ciągłe monitorowanie jakości w czasie rzeczywistym, co pozwala na natychmiastowe wykrywanie niezgodności i podejmowanie działań naprawczych. Dzięki temu przedsiębiorstwa mogą szybko reagować na potencjalne problemy, co z kolei zwiększa satysfakcję klientów oraz pozytywnie wpływa na reputację marki.
Jakie są różnice między automatyzacją a robotyzacją w przemyśle
Automatyzacja i robotyzacja to pojęcia często używane zamiennie, jednak mają one różne znaczenia i zastosowania w kontekście przemysłowym. Automatyzacja odnosi się do procesu wprowadzania technologii mających na celu zwiększenie efektywności produkcji poprzez eliminację lub ograniczenie interwencji człowieka. Może obejmować różnorodne systemy, takie jak oprogramowanie do zarządzania produkcją, automatyczne linie montażowe czy systemy kontroli jakości. Robotyzacja natomiast jest bardziej specyficznym terminem odnoszącym się do wykorzystania robotów przemysłowych w procesach produkcyjnych. Roboty mogą wykonywać różnorodne zadania, od prostych czynności takich jak pakowanie po bardziej skomplikowane operacje montażowe czy spawanie. Kluczową różnicą jest więc to, że robotyzacja jest jednym z elementów automatyzacji, ale nie obejmuje wszystkich aspektów tego procesu. W praktyce wiele firm decyduje się na połączenie obu podejść, aby maksymalizować korzyści płynące z nowoczesnych technologii.
Jakie są przykłady zastosowania automatyzacji w różnych branżach
Automatyzacja znajduje zastosowanie w wielu branżach przemysłowych, a jej implementacja przynosi wymierne korzyści w różnych obszarach działalności. W przemyśle motoryzacyjnym automatyzacja odgrywa kluczową rolę w procesie montażu pojazdów; roboty przemysłowe wykonują skomplikowane operacje spawania i malowania karoserii z dużą precyzją i szybkością. W branży spożywczej automatyzacja przyczynia się do zwiększenia wydajności linii produkcyjnych oraz poprawy jakości żywności poprzez kontrolę procesów pakowania i etykietowania. Z kolei w sektorze elektronicznym automatyzacja umożliwia masową produkcję komponentów elektronicznych przy zachowaniu wysokiej jakości oraz niskich kosztów produkcji. W logistyce automatyzacja pozwala na optymalizację procesów magazynowych; systemy zarządzania magazynem oraz autonomiczne pojazdy transportowe przyspieszają procesy załadunku i rozładunku towarów. Przemysł chemiczny również korzysta z automatyzacji poprzez zastosowanie systemów sterowania procesami chemicznymi, co zwiększa bezpieczeństwo oraz efektywność produkcji substancji chemicznych.
Jakie umiejętności są potrzebne do pracy w obszarze automatyzacji
Praca w obszarze automatyzacji wymaga od pracowników posiadania szeregu umiejętności technicznych oraz interpersonalnych. Kluczową umiejętnością jest znajomość technologii informacyjnej oraz programowania; wiele systemów automatyzacji opiera się na oprogramowaniu, które wymaga umiejętności kodowania oraz analizy danych. Wiedza z zakresu inżynierii mechanicznej i elektrycznej również jest istotna, ponieważ wiele urządzeń automatycznych łączy elementy obu tych dziedzin. Pracownicy muszą być także biegli w obsłudze narzędzi diagnostycznych oraz umieć przeprowadzać konserwacje maszyn i systemów automatycznych. Oprócz umiejętności technicznych ważne są także kompetencje miękkie; zdolność do pracy zespołowej oraz komunikacji z innymi członkami zespołu jest kluczowa dla skutecznego wdrażania projektów automatyzacyjnych. Umiejętność rozwiązywania problemów oraz kreatywność są również cenione w tej dziedzinie, ponieważ często pojawiają się nieprzewidziane wyzwania wymagające innowacyjnych rozwiązań.
Jakie są koszty wdrożenia automatyzacji w przemyśle
Koszt wdrożenia automatyzacji w przemyśle może być znaczny i zależy od wielu czynników, takich jak skala projektu, rodzaj technologii oraz specyfika branży. Na początku należy uwzględnić wydatki związane z zakupem sprzętu i oprogramowania; roboty przemysłowe czy systemy zarządzania produkcją mogą wiązać się z wysokimi kosztami początkowymi. Dodatkowo trzeba brać pod uwagę koszty instalacji oraz integracji nowych systemów z istniejącymi procesami produkcyjnymi; może to wymagać zatrudnienia specjalistów lub konsultantów zewnętrznych. Kolejnym istotnym aspektem są koszty szkoleń dla pracowników; aby zapewnić efektywne wykorzystanie nowych technologii, konieczne jest przeszkolenie zespołu odpowiedzialnego za ich obsługę. Należy także pamiętać o kosztach utrzymania systemów automatycznych; regularna konserwacja oraz aktualizacje oprogramowania mogą generować dodatkowe wydatki.
Jakie są najczęstsze błędy przy wdrażaniu automatyzacji
Wdrażanie automatyzacji w przemyśle wiąże się z wieloma wyzwaniami i pułapkami, które mogą prowadzić do niepowodzeń projektów. Jednym z najczęstszych błędów jest brak odpowiedniego planowania i analizy przed rozpoczęciem wdrożenia; przedsiębiorstwa często podejmują decyzje o inwestycji bez dokładnego zrozumienia swoich potrzeb oraz możliwości technologicznych. Kolejnym powszechnym problemem jest niedostateczne zaangażowanie pracowników; ignorowanie ich opinii oraz sugestii może prowadzić do oporu wobec zmian oraz niskiej akceptacji nowych technologii. Również niewłaściwe określenie celów projektu może skutkować brakiem mierzalnych rezultatów; przedsiębiorstwa powinny jasno definiować oczekiwania dotyczące efektywności oraz jakości przed rozpoczęciem wdrożenia. Inny błąd to zaniedbanie kwestii szkoleń dla pracowników; brak odpowiednich kompetencji może prowadzić do nieefektywnego wykorzystania nowych systemów oraz wzrostu liczby awarii maszyn.