Destylacja rozpuszczalników to proces, który polega na oddzieleniu składników mieszaniny na podstawie różnicy w ich temperaturach wrzenia. Jest to jedna z najstarszych i najczęściej stosowanych metod separacji substancji chemicznych. W praktyce proces ten może być realizowany na różne sposoby, w zależności od charakterystyki rozpuszczalników oraz wymagań dotyczących czystości końcowego produktu. Kluczowym elementem destylacji jest zastosowanie kolumny destylacyjnej, która umożliwia wielokrotne skraplanie i parowanie substancji, co zwiększa efektywność separacji. W przypadku rozpuszczalników organicznych, takich jak etanol czy aceton, ważne jest również uwzględnienie ich reakcji z innymi substancjami oraz ewentualnych zagrożeń związanych z ich stosowaniem. Proces destylacji można przeprowadzać zarówno w warunkach laboratoryjnych, jak i w przemyśle chemicznym, gdzie często wykorzystuje się bardziej zaawansowane technologie, takie jak destylacja frakcyjna czy próżniowa.
Jakie są różnice między destylacją a innymi metodami separacji
Destylacja rozpuszczalników różni się od innych metod separacji, takich jak ekstrakcja czy filtracja, przede wszystkim zasadą działania. Podczas gdy ekstrakcja polega na przenoszeniu substancji z jednej fazy do drugiej na podstawie ich rozpuszczalności, filtracja opiera się na mechanicznym oddzieleniu cząstek stałych od cieczy lub gazu. Destylacja natomiast wykorzystuje różnice w temperaturach wrzenia składników mieszaniny, co pozwala na ich selektywne oddzielanie. Warto również zauważyć, że destylacja jest szczególnie skuteczna w przypadku substancji lotnych, które łatwo parują i skraplają się. W przeciwieństwie do tego, metody takie jak chromatografia mogą być bardziej odpowiednie dla substancji o niskiej lotności lub dla mieszanin o skomplikowanej strukturze chemicznej. Ponadto, destylacja wymaga zastosowania specjalistycznego sprzętu i może być czasochłonna w porównaniu do prostszych technik separacyjnych.
Jakie są zastosowania destylacji rozpuszczalników w przemyśle
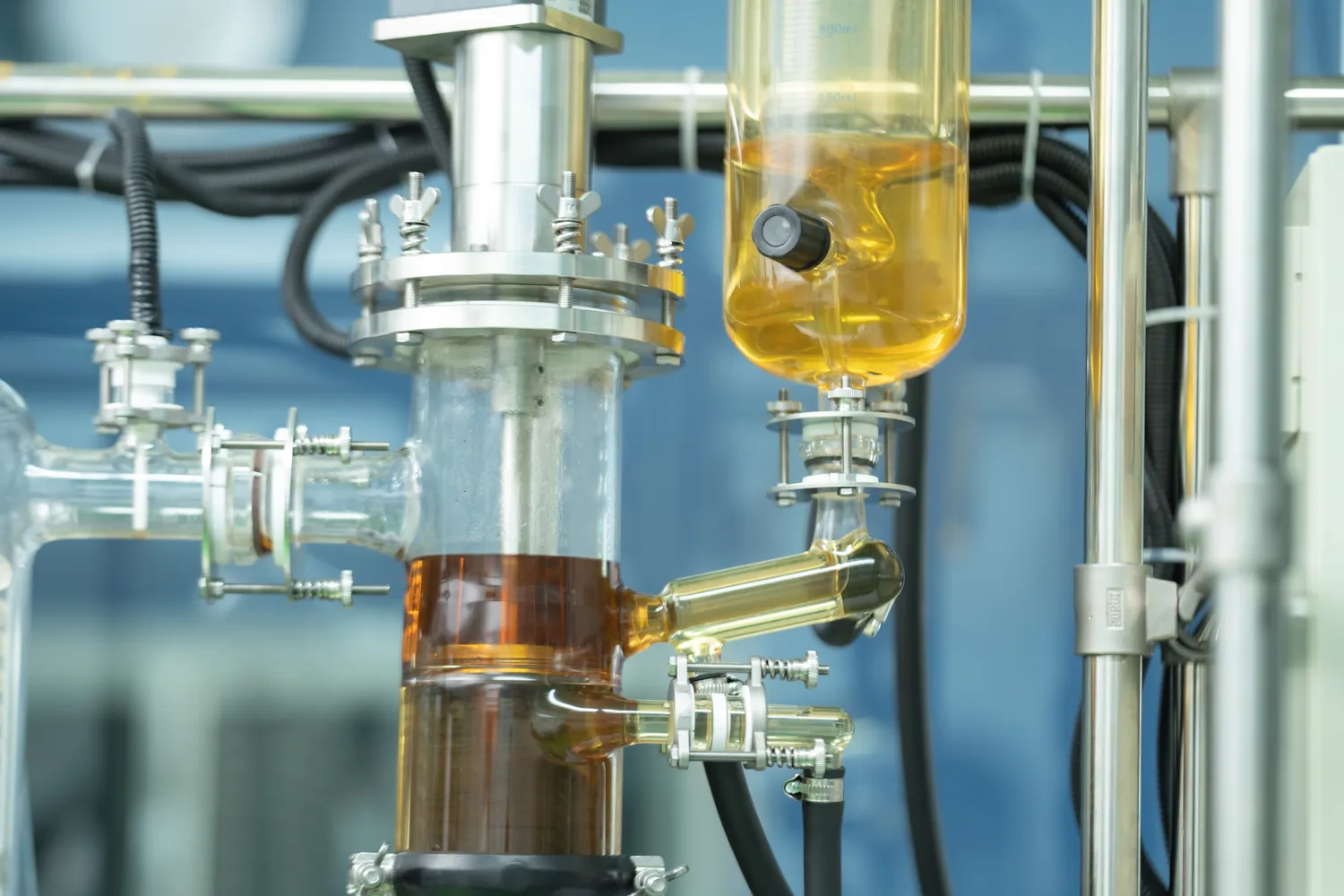
Destylacja rozpuszczalników ma szerokie zastosowanie w różnych gałęziach przemysłu chemicznego oraz farmaceutycznego. W przemyśle chemicznym proces ten jest kluczowy dla produkcji wielu substancji chemicznych, takich jak alkohole, ketony czy kwasy karboksylowe. Dzięki destylacji możliwe jest uzyskanie wysokiej czystości produktów końcowych, co jest niezbędne w dalszych procesach produkcyjnych. W branży farmaceutycznej destylacja jest wykorzystywana do oczyszczania surowców oraz produkcji leków o ściśle określonych wymaganiach jakościowych. Również w przemyśle spożywczym destylacja znajduje swoje miejsce – przykładem może być produkcja alkoholi wysokoprocentowych czy aromatów naturalnych. W ostatnich latach rośnie zainteresowanie ekologicznymi metodami destylacji, które mają na celu zmniejszenie zużycia energii oraz minimalizację odpadów. Nowoczesne technologie pozwalają na optymalizację procesu destylacji poprzez zastosowanie systemów odzysku ciepła oraz automatyzację procesów kontrolnych.
Jakie są najczęstsze problemy podczas destylacji rozpuszczalników
Podczas procesu destylacji rozpuszczalników mogą wystąpić różnorodne problemy, które mogą wpływać na efektywność separacji oraz jakość uzyskanego produktu. Jednym z najczęstszych problemów jest tzw. „przegrzewanie”, które może prowadzić do niepożądanych reakcji chemicznych oraz obniżenia czystości końcowego produktu. Innym istotnym zagadnieniem jest kontrola temperatury – niewłaściwe ustawienia mogą spowodować niepełną separację składników lub ich niezamierzone mieszanie się. Dodatkowo w przypadku destylacji frakcyjnej konieczne jest precyzyjne dobranie kolumny destylacyjnej oraz odpowiednich warunków operacyjnych, aby uzyskać pożądane frakcje. Problemy mogą również wynikać z jakości używanych surowców – obecność zanieczyszczeń może negatywnie wpłynąć na przebieg procesu oraz jakość otrzymywanych produktów. Ważnym aspektem jest także bezpieczeństwo pracy podczas prowadzenia procesów destylacyjnych ze względu na potencjalne ryzyko związane z obsługą substancji łatwopalnych czy toksycznych.
Jakie są różne metody destylacji rozpuszczalników w praktyce
W praktyce istnieje wiele różnych metod destylacji rozpuszczalników, które można dostosować do specyficznych potrzeb i charakterystyki separowanych substancji. Najpopularniejszą z nich jest destylacja prosta, która polega na podgrzewaniu cieczy do momentu jej wrzenia, a następnie skraplaniu powstałych par. Ta metoda jest najczęściej stosowana w przypadku jednofazowych mieszanin o znacznej różnicy temperatur wrzenia składników. Kolejną techniką jest destylacja frakcyjna, która umożliwia oddzielanie wielu składników o zbliżonych temperaturach wrzenia. W tym przypadku wykorzystuje się kolumnę destylacyjną, która zwiększa powierzchnię wymiany ciepła i pozwala na wielokrotne skraplanie i parowanie. Istnieją również bardziej zaawansowane metody, takie jak destylacja próżniowa, która jest stosowana w przypadku substancji wrażliwych na wysoką temperaturę. Obniżenie ciśnienia pozwala na obniżenie temperatury wrzenia, co minimalizuje ryzyko degradacji termicznej. Innym podejściem jest destylacja azeotropowa, która wykorzystuje dodatkowe substancje do zmiany właściwości mieszaniny i umożliwienia separacji składników tworzących azeotrop.
Jakie są kluczowe czynniki wpływające na efektywność destylacji
Efektywność destylacji rozpuszczalników zależy od wielu czynników, które mogą znacząco wpłynąć na jakość i ilość uzyskiwanego produktu. Jednym z najważniejszych aspektów jest temperatura wrzenia poszczególnych składników mieszanki. Różnice w temperaturach wrzenia decydują o tym, jakie substancje będą parować jako pierwsze i w jakiej kolejności będą oddzielane. Kolejnym istotnym czynnikiem jest ciśnienie atmosferyczne – obniżenie ciśnienia może prowadzić do obniżenia temperatury wrzenia, co może być korzystne w przypadku substancji wrażliwych na wysoką temperaturę. Ważna jest także konstrukcja kolumny destylacyjnej oraz jej parametry operacyjne, takie jak wysokość kolumny czy liczba teoretycznych półek, które wpływają na efektywność separacji. Dodatkowo jakość używanych surowców ma kluczowe znaczenie – obecność zanieczyszczeń może negatywnie wpłynąć na proces destylacji oraz jakość końcowego produktu. Odpowiednia kontrola parametrów procesu oraz regularne monitorowanie jakości surowców są niezbędne dla uzyskania optymalnych wyników.
Jakie są najnowsze technologie w dziedzinie destylacji
W ostatnich latach rozwój technologii związanych z destylacją rozpuszczalników przyniósł wiele innowacyjnych rozwiązań, które mają na celu zwiększenie efektywności procesów separacyjnych oraz redukcję kosztów produkcji. Jednym z takich rozwiązań jest zastosowanie technologii membranowych, które mogą stanowić alternatywę dla tradycyjnych metod destylacji. Membrany selektywnie przepuszczają określone składniki mieszaniny, co pozwala na ich oddzielanie bez konieczności podgrzewania. Innym nowoczesnym podejściem jest wykorzystanie nanotechnologii do tworzenia materiałów o wyjątkowych właściwościach separacyjnych, które mogą poprawić wydajność procesów destylacyjnych. Zastosowanie sztucznej inteligencji i algorytmów uczenia maszynowego w monitorowaniu i optymalizacji procesów również staje się coraz bardziej popularne. Dzięki analizie danych w czasie rzeczywistym możliwe jest szybkie dostosowywanie parametrów operacyjnych do zmieniających się warunków pracy, co przekłada się na lepsze wyniki produkcyjne.
Jakie są aspekty ekologiczne związane z destylacją rozpuszczalników
Aspekty ekologiczne związane z destylacją rozpuszczalników stają się coraz ważniejsze w kontekście rosnącej świadomości społecznej dotyczącej ochrony środowiska oraz zrównoważonego rozwoju przemysłu chemicznego. Procesy destylacyjne często wiążą się z dużym zużyciem energii oraz emisją gazów cieplarnianych, dlatego kluczowe znaczenie ma wdrażanie technologii mających na celu minimalizację tych negatywnych skutków. Przykładem mogą być systemy odzysku ciepła, które pozwalają na ponowne wykorzystanie energii generowanej podczas procesu destylacji, co przyczynia się do obniżenia kosztów operacyjnych oraz zmniejszenia emisji CO2. Ponadto coraz większą uwagę zwraca się na wykorzystanie odnawialnych źródeł energii w procesach przemysłowych, co może znacząco wpłynąć na ich ekologiczny bilans. Warto również wspomnieć o konieczności odpowiedniego zarządzania odpadami powstającymi podczas procesów destylacyjnych – niektóre substancje mogą być toksyczne lub szkodliwe dla środowiska, dlatego ich utylizacja musi odbywać się zgodnie z obowiązującymi normami prawnymi oraz najlepszymi praktykami ekologicznymi.
Jakie są przyszłe kierunki rozwoju technologii destylacji
Przyszłość technologii destylacji rozpuszczalników zapowiada się obiecująco dzięki ciągłemu postępowi naukowemu oraz technologicznemu. W miarę jak rośnie potrzeba bardziej efektywnych i ekologicznych procesów produkcyjnych, badacze i inżynierowie pracują nad innowacyjnymi rozwiązaniami mającymi na celu poprawę wydajności i redukcję kosztów operacyjnych. Jednym z kluczowych kierunków rozwoju jest integracja różnych metod separacyjnych – połączenie destylacji z innymi technikami takimi jak ekstrakcja czy chromatografia może prowadzić do uzyskania lepszych wyników separacyjnych oraz wyższej czystości produktów końcowych. Również rozwój materiałów o unikalnych właściwościach fizykochemicznych może otworzyć nowe możliwości dla efektywnej separacji substancji chemicznych. W kontekście zmian klimatycznych oraz rosnących wymagań dotyczących ochrony środowiska coraz większy nacisk kładzie się także na zrównoważony rozwój procesów przemysłowych – technologie oparte na odnawialnych źródłach energii oraz minimalizacja odpadów będą miały kluczowe znaczenie dla przyszłości przemysłu chemicznego.